1. Аксідная плёнка:
Алюміній вельмі лёгка акісляецца на паветры і пры зварцы. Атрыманы аксід алюмінію (Al2O3) мае высокую тэмпературу плаўлення, вельмі стабільны і яго цяжка выдаліць. Гэта перашкаджае плаўленню і зліванню зыходнага матэрыялу. Аксідная плёнка мае высокую ўдзельную вагу і нялёгка ўсплывае на паверхню. Лёгка стварыць дэфекты, такія як шлакавыя ўключэнні, няпоўнае плаўленне і няпоўнае пранікненне.
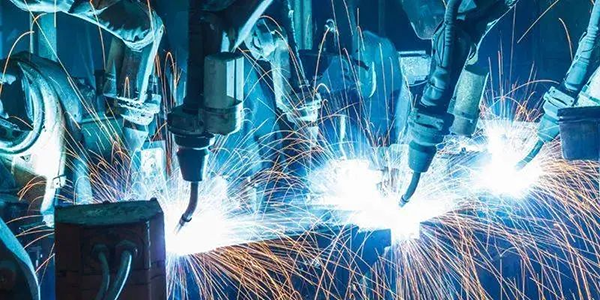
Паверхневая аксідная плёнка алюмінія і паглынанне вялікай колькасці вільгаці могуць лёгка выклікаць пары ў зварным шве. Перад зваркай трэба выкарыстоўваць хімічныя або механічныя метады для строгай ачысткі паверхні і выдалення павярхоўнай аксіднай плёнкі.
Узмацніце абарону ў працэсе зваркі, каб прадухіліць акісленне. Пры выкарыстанні вальфрамавай зваркі ў інертным газе выкарыстоўвайце сетку пераменнага току, каб выдаліць аксідную плёнку праз эфект "ачысткі катода".
Пры выкарыстанні газавай зваркі выкарыстоўвайце флюс, які выдаляе аксідную плёнку. Пры зварцы тоўстых пласцін можна павялічыць нагрэў зваркі. Напрыклад, геліевая дуга мае вялікі нагрэў, і для абароны выкарыстоўваецца гелій або аргона-геліевая сумесь газу, або выкарыстоўваецца буйнамаштабная зварка плаўленым электродам у абароненым газе. У выпадку станоўчага злучэння пастаяннага току «катодная ачыстка» не патрабуецца.
2. Высокая цеплаправоднасць
Цеплаправоднасць і ўдзельная цеплаёмістасць алюмінія і алюмініевых сплаваў прыкладна ўдвая больш, чым у вугляродзістай сталі і нізкалегаванай сталі. Каэфіцыент цеплаправоднасці алюмінія больш чым у дзесяць разоў перавышае паказчык аўстэнітнай нержавеючай сталі.
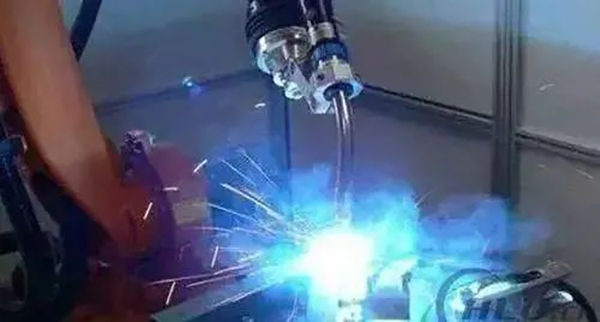
У працэсе зваркі вялікая колькасць цяпла можа хутка перадавацца ў асноўны метал. Такім чынам, пры зварцы алюмінія і алюмініевых сплаваў, у дадатак да энергіі, якая спажываецца ў басейне расплаўленага металу, больш цяпла таксама спажываецца без неабходнасці ў іншых частках металу. Гэта Спажыванне гэтага віду бескарыснай энергіі больш значнае, чым пры зварцы сталі. Для атрымання высакаякасных зварных злучэнняў неабходна максімальна выкарыстоўваць энергію з канцэнтраванай энергіяй і высокай магутнасцю, а часам таксама можна выкарыстоўваць папярэдні нагрэў і іншыя тэхналагічныя меры.
3. Вялікі каэфіцыент лінейнага пашырэння, лёгка дэфармуецца і стварае цеплавыя расколіны
Каэфіцыент лінейнага пашырэння алюмінія і алюмініевых сплаваў прыкладна ўдвая большы, чым у вугляродзістай сталі і нізкалегаванай сталі. Аб'ёмная ўсаджванне алюмінія падчас застывання вялікая, а дэфармацыя і напружанне зварнога шва вялікія. Такім чынам, неабходна прыняць меры для прадухілення зварачных дэфармацый.
Калі алюмініевая зварачная расплаўленая ванна застывае, лёгка ствараць усаджвальныя паражніны, усаджвальную сітаватасць, гарачыя расколіны і высокае ўнутранае напружанне.
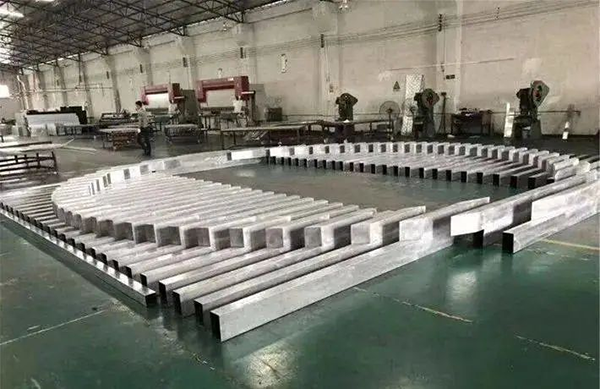
Зварачнае абсталяванне Xinfa мае характарыстыкі высокай якасці і нізкай цаны. Для атрымання падрабязнай інфармацыі, калі ласка, наведайце:Вытворцы зваркі і рэзкі - Кітайская фабрыка і пастаўшчыкі зваркі і рэзкі (xinfatools.com)
Могуць быць прыняты меры для карэкціроўкі складу зварачнага дроту і працэсу зваркі, каб прадухіліць з'яўленне гарачых расколін падчас вытворчасці. Калі дазваляе ўстойлівасць да карозіі, зварачны дрот з алюмініева-крэмніевага сплаву можна выкарыстоўваць для зваркі алюмініевых сплаваў, акрамя алюмініева-магніевых. Калі алюмініева-крэмніевы сплаў змяшчае 0,5% крэмнія, тэндэнцыя да гарачых расколін большая. Па меры павелічэння ўтрымання крэмнію дыяпазон тэмператур крышталізацыі сплаву становіцца меншым, цякучасць значна павялічваецца, хуткасць ўсаджвання памяншаецца, і адпаведна памяншаецца тэндэнцыя да адукацыі гарачых расколін.
Згодна з вопытам вытворчасці, гарачае парэпанне не адбудзецца, калі ўтрыманне крэмнію складае ад 5% да 6%, таму выкарыстанне стужкі SAlSi (утрыманне крэмнія ад 4,5% да 6%) зварачнага дроту будзе мець лепшую ўстойлівасць да расколінаў.
4. Лёгка растварае вадарод
Алюміній і алюмініевыя сплавы могуць раствараць вялікую колькасць вадароду ў вадкім стане, але амаль не раствараюць вадарод у цвёрдым стане. У працэсе зацвярдзення і хуткага астуджэння зварачнай ванны вадарод не паспявае выходзіць, і лёгка ўтвараюцца вадародныя дзіркі. Вільгаць у атмасферы слупа дугі, вільгаць, адсарбаваная аксіднай плёнкай на паверхні зварачнага матэрыялу і асноўнага металу, з'яўляюцца важнымі крыніцамі вадароду ў зварным шве. Такім чынам, крыніца вадароду неабходна строга кантраляваць, каб прадухіліць адукацыю пор.
5. Стыкі і зоны тэрмічнага ўздзеяння лёгка размягчаются
Элементы сплаву лёгка выпараюцца і гараць, што зніжае характарыстыкі зварнога шва.
Калі асноўны метал дэфармацыйна ўмацаваны або ўмацаваны цвёрдым растворам, нагрэў зваркі знізіць трываласць зоны тэрмічнага ўздзеяння.
Алюміній мае гранецэнтрычную кубічную рашотку і не мае алатропаў. Няма змены фазы падчас нагрэву і астуджэння. Зярністасць зварнога шва, як правіла, становіцца грубай, і збожжа не можа быць ачышчана з дапамогай змены фазы.
Спосаб зваркі
Для зваркі алюмінія і алюмініевых сплаваў можна выкарыстоўваць практычна розныя метады зваркі, але алюміній і алюмініевыя сплавы па-рознаму прыстасоўваюцца да розных метадаў зваркі, і розныя метады зваркі маюць свае ўласныя выпадкі прымянення.
Метады газавай зваркі і электродной дуговой зваркі простыя ў абсталяванні і простыя ў эксплуатацыі. Газавая зварка можа выкарыстоўвацца для рамонтнай зваркі алюмініевых лістоў і адлівак, якія не патрабуюць высокай якасці зваркі. Дугавая зварка электродам можа прымяняцца для рамонтнай зваркі адлівак з алюмініевых сплаваў.
Метад зваркі ў абароненым газе (TIG або MIG) з'яўляецца найбольш шырока выкарыстоўваным метадам зваркі алюмінія і алюмініевых сплаваў.
Лісты алюмінія і алюмініевых сплаваў можна зварваць аргонадугавой зваркай вальфрамавым электродам пераменным токам або аргонадугавой зваркай вальфрамавым электродам.
Алюміній і тоўстыя пласціны з алюмініевых сплаваў можна апрацоўваць вальфрамавай гелиевой дуговой зваркай, аргон-гелиевой змешанай вальфрамавай дуговой зваркай, газавай дуговой зваркай металу і імпульснай дуговой зваркай металу. Усё шырэй прымяняюцца газадугавая зварка металаў і імпульсная газадугавая зварка металаў.
Час публікацыі: 25 ліпеня 2024 г